Effective inventory management is essential in food manufacturing facilities – particularly for plant workers’ PPE, Jansan supplies, lab materials, equipment repair tools and other consumables. Real-time inventory analytics offers a way to track these critical items, optimize operations, and maintain a safe working environment.
The importance of real-time data for essential supplies
Real-time inventory tracking provides immediate insights into stock levels, which allows for proactive decision-making. This constant monitoring is essential for reducing waste and minimizing disruptions to production.
“By utilizing real-time data, food processing companies can ensure they have the necessary materials and equipment readily available, supporting both efficiency and safety.”
Why real-time analytics is crucial
The food processing and manufacturing industry faces unique challenges that make real-time inventory analytics for these supplies particularly valuable:
- Stringent Regulations: The food industry must adhere to strict cleanliness and safety standards. Real-time analytics assists in maintaining compliance, reducing contamination risks, and ensuring workplace safety.
- Safety: Having the right PPE and tools available is essential for preventing accidents and injuries.
- Variable Usage: The demand for supplies and tools can fluctuate based on production needs and maintenance schedules, and real-time data helps companies adapt to these changes.
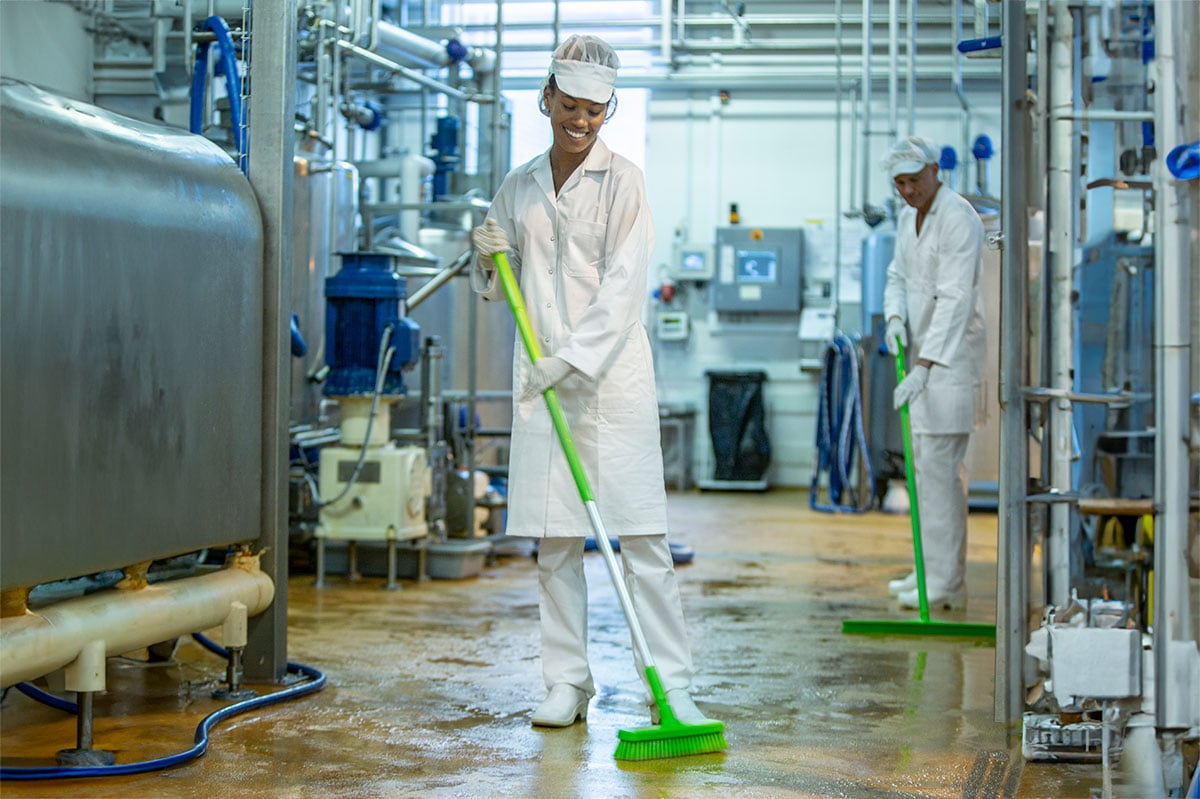
Key components of real-time inventory analytics for essential items
A robust real-time inventory system should monitor all crucial aspects of your operation, including:
- Jansan Supplies: Monitoring the levels of cleaning supplies, such as hand sanitizer, hand soap, paper towels, and cleaning chemicals, is vital for maintaining a hygienic production environment.
- Laboratory Materials: Tracking laboratory and quality control materials helps ensure food safety.
- Personal Protective Equipment (PPE): Real-time tracking of PPE, including boots, gloves, safety glasses, hard hats, and safety clothing, ensures worker protection and regulatory compliance.
- Service and Repair Tools: Monitoring the availability of essential tools ensures that equipment maintenance and repairs can be performed quickly, preventing production delays.
Benefits of real-time analytics for these specific categories
Implementing real-time data analytics into inventory management provides several benefits:
- Improved Safety: Ensuring that jan san, lab, and PPE supplies are always available contributes to a safe working environment.
- Reduced Downtime: Real-time insights into the availability of tools facilitate efficient maintenance and repairs, thereby minimizing downtime.
- Enhanced Traceability: Real-time tracking enhances visibility, allowing for the rapid identification and resolution of issues.
- Better Decision-Making: Immediate access to data enables informed decisions and a proactive response to changes, thus optimizing operations.
- Improved Compliance: Real-time monitoring ensures adherence to regulatory standards for hygiene and safety.
- Cost Savings: Real-time analytics can reduce waste, lower carrying costs, and minimize the risks of stockouts.
- Enhanced Productivity: Real-time insights facilitate streamlined operations and optimized resource allocation, boosting productivity and minimizing downtime.
Key features of an effective real-time inventory system
A successful real-time inventory management system should have the following features:
- Automated Data Collection: Automated data capture reduces manual tracking and human error.
- Data Integration: Seamless integration with existing systems ensures accurate, real-time data exchange.
- Real-Time Dashboards: Visual representations of inventory levels and key performance indicators (KPIs) provide at-a-glance insights.
- Alerts and Notifications: Automated alerts notify users of low stock levels or other critical issues.
- Customizable Reporting: Detailed, tailored reports provide the information needed to analyze trends and optimize inventory.
SupplyRITE™ Inventory Solutions
SupplyRITE™ Inventory Solutions are designed to meet the unique needs of the food processing industry. Services include:
- Industrial Vending Machines: Automated dispensing of PPE, cleaning supplies, lab materials, and tools ensures 24/7 availability.
- Customer-Managed Inventory: Analysis of purchase history and establishment of efficient ordering methods to help you manage your own inventory.
- Vendor-Managed Inventory (VMI): Data-driven management of your inventory by experts who ensure products are available when needed.
- Expert Consultation: Process reviews and identification of improvement opportunities from industry experts.
- Continuous Improvement: Evaluation of inventory solutions and provision of ongoing support and feedback.
Embracing the future
By implementing real-time inventory analytics, food processing companies can improve safety, enhance compliance, optimize operations, and achieve long-term success. Companies like Nelson-Jameson provide the support and expertise to ensure optimal inventory management for your specific needs.
Adam Reno
Inventory Solutions Department Manager
Adam is a 10-year veteran of the food manufacturing industry and builds strong customer relationships through customized CMI/VMI solutions, optimizing customer inventory and streamlining operations.