Ready for Launch: Helping Streamline Food Manufacturers' Start Up Operations
The Background
Nelson-Jameson supported Suntado with tailored industry expertise in the launch of a new food manufacturing facility. The launch included implementing programs for food safety, sanitation, and operations.
Nelson-Jameson provided industry-vetted products and solutions to Suntado to help optimize processes across the facility, from lab testing to inventory management. This support helped streamline Suntado’s start up operations and ensured ongoing operational efficiency. Through 22 weeks of dedicated assessment meetings, Nelson-Jameson saved the plant seven hours per week on product sourcing and streamlined purchase orders, resulting in $30,000 annual savings.
Better visibility of inventory metrics supported proactive decision-making for sustained cost savings and operational excellence. Nelson-Jameson’s collaboration with Suntado exemplified a strong, supportive partnership driving long-term success.
-
Seven hours saved each week
-
$30k in annual savings
-
Qualified for QCS Rebate
Seven hours saved each week
$30k in annual savings
Allowed QCS-driven rebate to be earned
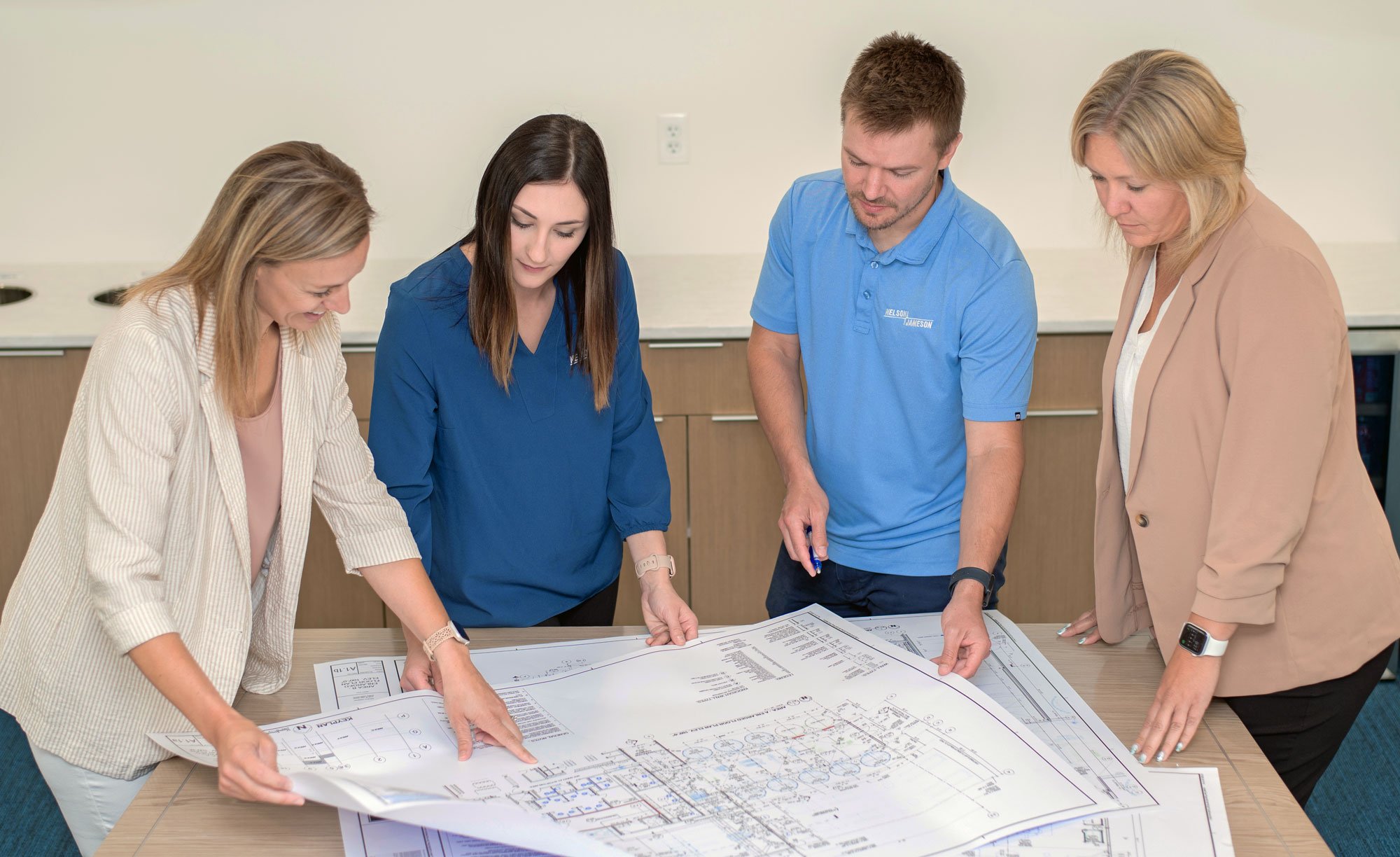
The Challenge
Nelson-Jameson aimed to provide industry knowledge, support, and consultation to Suntado for the creation and start up of a food manufacturing facility. The primary objective was to ensure the successful establishment and comprehensive operational readiness of the new plant, both directly and indirectly.
Nelson-Jameson focused on developing and implementing key programs for color-coding, signage, sanitation, PPE, lab testing, inventory management, and preventative maintenance. It would offer technical support for selecting and installing equipment and processes tailored to the plant’s needs. These objectives were crucial to both parties; for Nelson-Jameson, to strengthen an industry partnership and for Suntado, to achieve a seamless start up and sustained operational success.
Nelson-Jameson’s commitment to delivering the exceptional for Suntado would be demonstrated through continued support beyond the plant’s opening to underscore the strategic partnership and commitment to long-term success.
The Solution
Our Approach
Nelson-Jameson collaborated with Suntado to offer a full range of products and programs, creating decision-making systems that streamline plant start up and ensure smooth operations.
Best Practices and Systems
Leveraging its technical experts and supplier partners, Nelson-Jameson provided best practices in color-coded tooling, lab testing, inventory management, ingredient channels, and maintenance systems. It also offered strategic programs, like logistics, local inventory, service partnerships, and third-party warehousing.
Innovated Inventory Management
Nelson-Jameson implemented an innovative inventory management program using technology to optimize onsite inventory of lab supplies, plant consumables, and maintenance spares. It addressed challenges like aligning inventory with expanding production needs, through reporting visibility and consistent communication with Suntado.
A Trusted, Ongoing Relationship
Nelson-Jameson’s proactive approach built trust and fostered a mutually beneficial partnership with ongoing support as the plant commissioned and expands production.
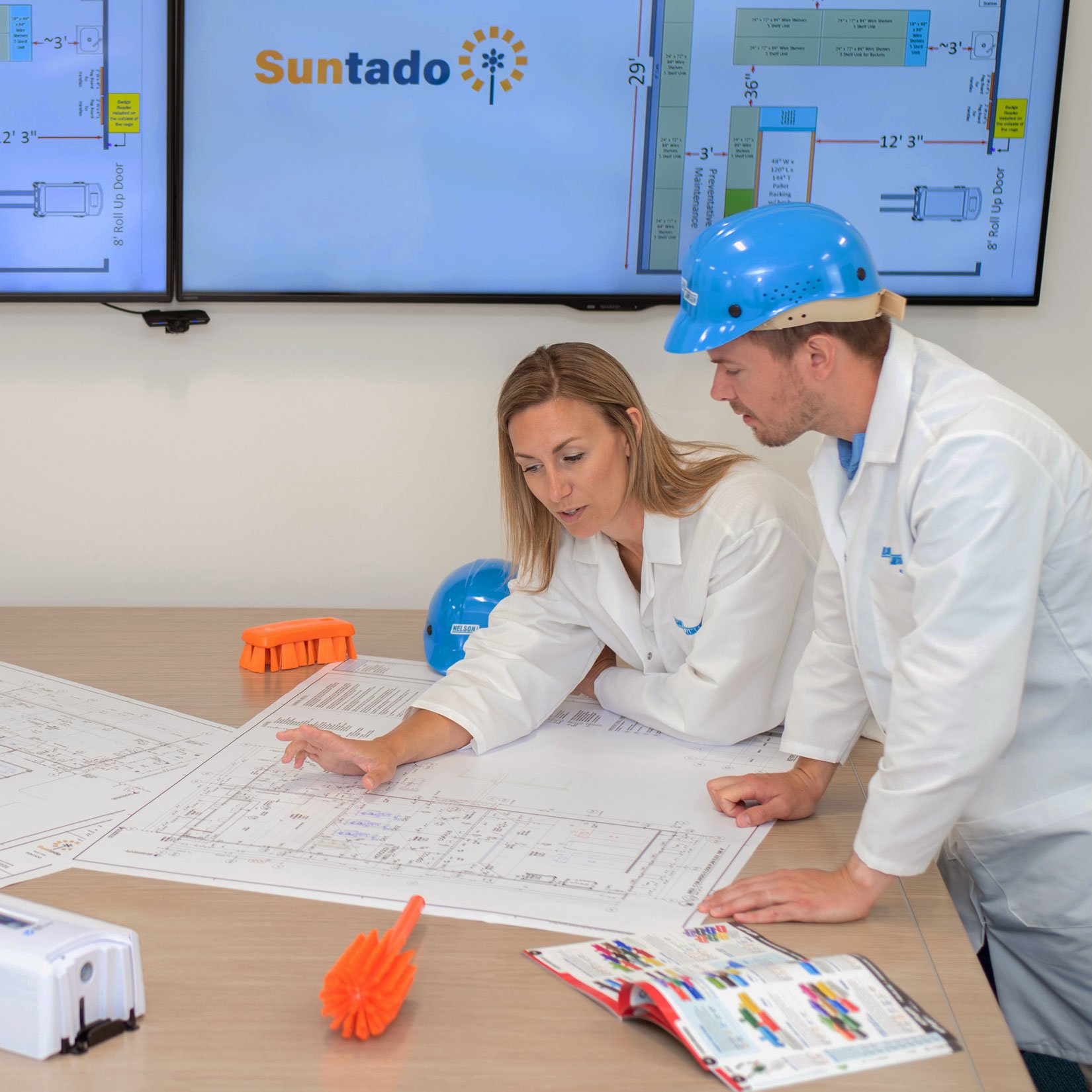
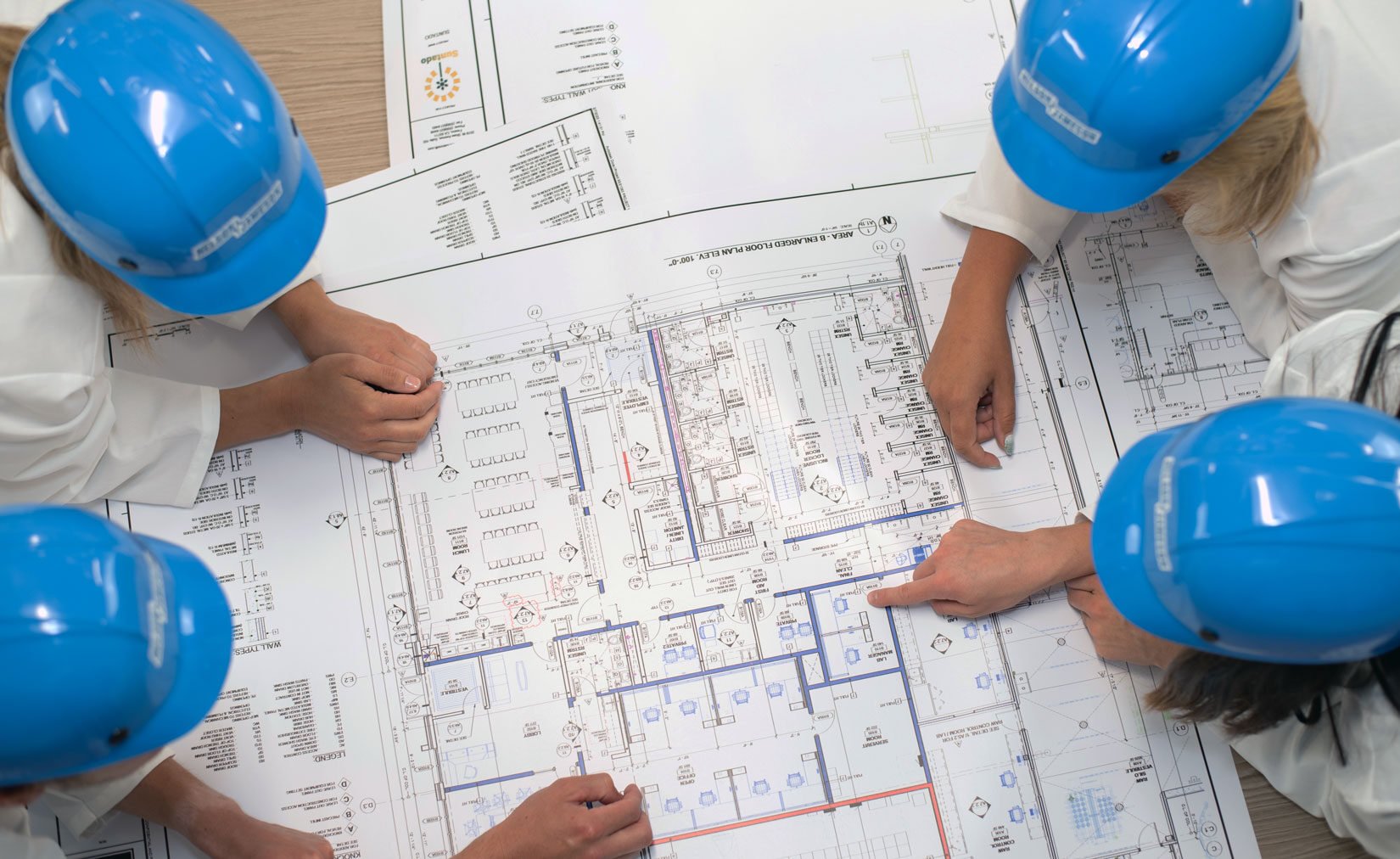
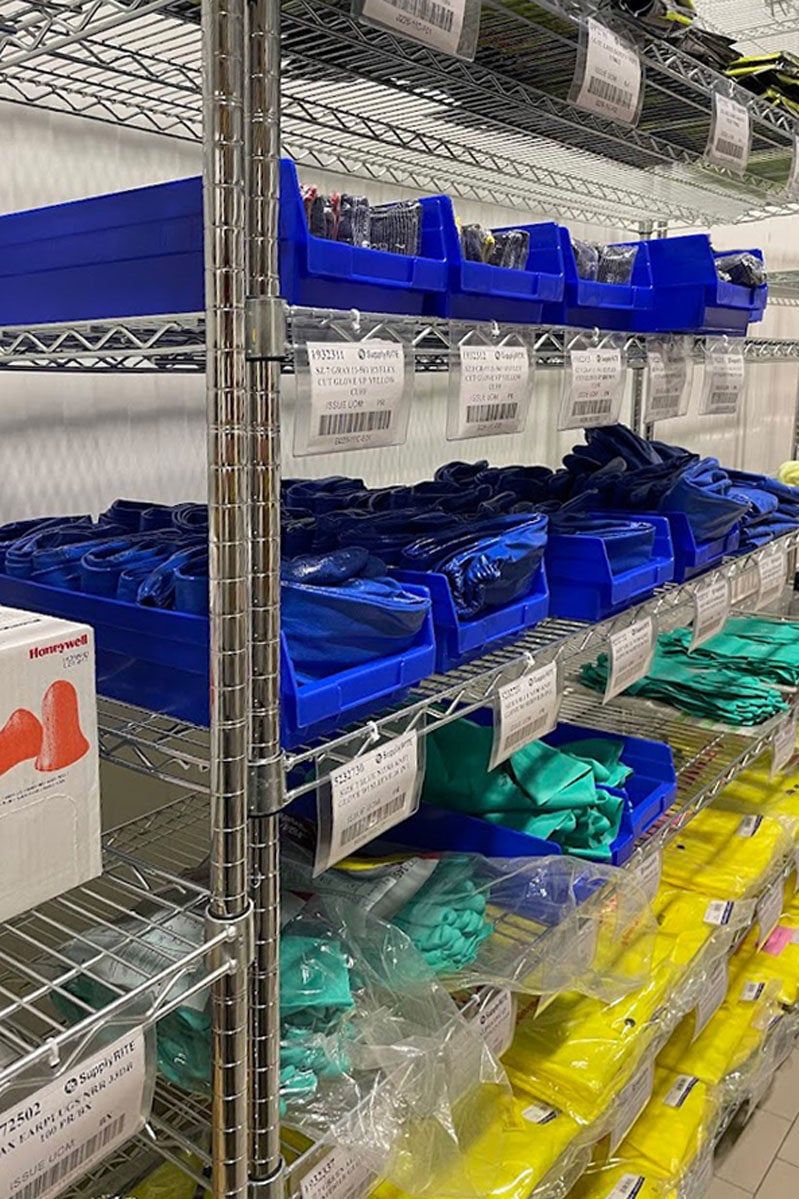
The Results
The collaboration between Nelson-Jameson and Suntado has delivered significant value and notable outcomes. Implementing the SupplyRITE™ Inventory Solutions program streamlined operations in the laboratory, plant consumables, and maintenance, saving an estimated $30,000 annually on Purchase Order reduction, not including savings on order placement and receiving labor, PO tracking, and supplier management.
It minimized stockouts, enhancing logistics efficiency for measurable cost reductions like a full-time inventory employee. Nelson-Jameson’s expertise in inventory management and vending solutions provided Suntado with enhanced visibility into inventory metrics like forecasting, deadstock, and urgent needs, enabling proactive inventory management and strategic decision-making.
Long-term benefits include sustained cost savings, improved supply chain effectiveness, and streamlined operations, fostering a robust partnership across every department from the C-Suite to plant operations.
Suntado greatly benefited from working with Nelson-Jameson’s SupplyRITE™ inventory management team during its Greenfield planning and plant start up. The team provided turnkey parts inventory solutions instrumental in our successful launch. Their expertise in inventory control, procurement, and forecasting ensured we had the right parts available when needed, minimizing downtime and enhancing operational efficiency. This partnership was invaluable in establishing a reliable and efficient inventory management system, contributing significantly to Suntado’s smooth start up and ongoing success. Beau Lewis, Maintenance Manager |