Nelson-Jameson Improves Cheesemaker’s Quality, Efficiency with Custom Autobagger Tubing
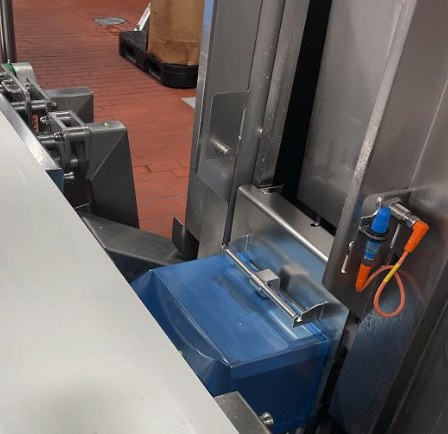
Industry
Dairy
Challenge
A Wisconsin dairy manufacturer saw frequent leading and bubbling issues with its bags when packaging its 40-lb blocks. These issues impacted quality, and led to inefficiency and unnecessary waste.
Results
Nelson-Jameson provided a high-quality, customized bagging solution along with pre- and post-purchase assistance. The new bagging and expert support helped achieve a more effective bagging process and reduced the manufacturer’s costs.
Solution
Custom Autobagger Tubing
Nelson-Jameson doesn’t just provide what they determine to be the best solution for our unique needs. The entire team listens to our feedback and incorporates that information into a tailored solution that works best for us.
Packaging Engineer
Wisconsin cheese manufacturer
Nelson-Jameson and their manufacturer were so easy to work with and took our opinions back to the technical team to improve the film performance.
Packaging Technician
Texas cheese and whey processor
The Challenge
An award-winning, Wisconsin-based dairy manufacturer experienced consistent leaks, splitting, and bubbling when utilizing its Tetra Pak Automatic Bag Former to package its nearly 22,500 daily 40-lb blocks of cheese. These leaks had led to gas and moisture exchange that can affect the aroma and flavor of cheese, and its current bagging solution simply didn’t have enough stretch and tolerance to yield consistently sealed results for its cheese which is mostly sold in bulk.
In addition to this challenge, its bags were purchased from an overseas source that shipped only by container loads, adding additional logistical time and costs to its process. As a result of the costs and inefficiency, the dairy manufacturer needed seamlessly integrate a new tubing option for its blocks of cheese that had the strength and sealing efficiency to yield consistent results.
The Solution
Nelson-Jameson partnered with the Wisconsin cheesemaker to assess its specific needs and develop a tailored approach that included sourcing customized autobagger tubing, cost-saving implementation guidance, and ongoing training and technical support.
The bagging solution Nelson-Jameson provided is a domestically sourced, high-performance tubing designed for use with Tetra Pak autobagger systems. The tubing is engineered to improve efficiency, reduce manual labor, and provide a superior packaging solution for the 40-pound blocks of cheese that the cheesemaker primarily produces.
Its strong yet thin skin barrier is the new standard in cheese block packaging, with an advanced, high-performance design engineered to meet the unique packaging demands in the food manufacturing industry. The autobagger tubing’s premium packaging film combines tensile strength with optimal sealing efficiency. This specialized cheese packaging also incorporates anti-static properties, minimizing the risks associated with static electricity, effectively dissipating static charge, and preventing product contamination, packaging damage, and potential safety hazards.
Trial and Implementation
Nelson-Jameson began the partnership by identifying the custom width and length needed for the cheesemaker’s 40-pound blocks. Once the dimensions were incorporated into the autobagger tubing, Nelson-Jameson and a manufacturer representative went on-site to bring a trial roll in to test, make recommendations, and observe the final product before and after the blocks were sealed.
Based on that information, the Nelson-Jameson team then suggested improvements before ramping up the trial with four rolls. This step ensured consistency and that the cheesemaker was comfortable with the final result before scaling its order to multiple pallets on a cadence that met its needs.
Ongoing Support
The partnership didn’t end with the delivery of its first full pallet. Nelson-Jameson offers on-demand support from a machine technician who continues to work with the bag manufacturer to provide on-site assistance for the cheesemaker. This ensures smooth operation and promptly addresses future issues. The continued support provides unmatched industry expertise and experience to fulfill any troubleshooting or optimization needs or questions that might arise to maximize efficiency and minimize downtime.
The Results
By incorporating the Nelson-Jameson high-barrier autobagger solution, the cheesemaker was able to reduce leaking issues by more than 50% with a vacuum-tight seal. This resulted in a better end product for the consumer while increasing its efficiency by reducing cheese-trimming waste, decreasing downtime, and producing more bags per minute. The new tubing solution created an estimated $75,000 in annual cost savings and saved about 2,000 labor hours.
With domestic sourcing and ongoing post-purchase support, the Wisconsin cheesemaker decreases its lead time, reliably maintains its autobagger tubing supply, and leverages Nelson-Jameson expertise to ensure smooth operation with minimal downtime.